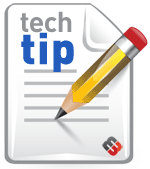
Stress management is critical for adhesive applications, mainly due to the possibility of a CTE (coefficient of thermal expansion) mismatch between the substrates being bonded, and between the substrates and the adhesive. Even in assemblies where similar substrates are being bonded, the thermo-mechanical stress on bonded joints plays a critical role, since the adhesive layer may expand and contract at a different rate, as compared to the substrates. This is accentuated even further in applications involving dissimilar substrates, with differences in their thermal expansion coefficients.
One of the approaches to mitigate the differences in thermal expansion, is to select an adhesive with as low thermal expansion coefficient as possible. For an unfilled, rigid / stiff epoxy, the CTE might hover at around 40-50 ppm/C at room temperature. This CTE can be reduced through the use of ceramic or specialty negative coefficient of thermal expansion fillers, to values as low as 10 ppm/C at room temperature. It should be noted that adding such fillers in adhesives increases the modulus significantly. For example, the tensile modulus of an unfilled, relatively rigid two component epoxy can range anywhere from 350,000-450,000 psi at room temperature, but adding fillers may increase this value in some cases to around 2 to 3 times. Therefore, typically, adhesives with very low CTE’s tend to be stiffer.
Stress-Strain Curve for Low CTE Epoxy EP17HTND-CCM
The other approach to reduce stress on the bond joint is to utilize rubber toughened or “flexibilized” adhesive systems. These adhesives offer a toughened cure, and some of them have been known to offer relatively high lap shear strength (for aluminum-aluminum bond), in excess of 1000 psi, with a tensile modulus in some cases not higher than 50,000 psi. Some of these systems also provide relatively high elongation values, ranging from 20 % to 100 % or even higher. Such products offer a higher thermal expansion coefficient, which could be around 80-150 ppm/C at room temperature.
Stress-Strain Curve for Higher CTE Epoxy EP40Med
Although there is no “standardized” process to select adhesives to manage thermo-mechanical stresses, typically, the more rigorous the thermal cycling & ramp rates, the more the tendency to lean towards using a lower modulus, slightly more forgiving adhesive system. However, based on the severity of the thermal stresses, the ramp rates, the dwell times at the extremes, and the mechanical properties desired, design engineers must be cognizant to weigh the benefits and tradeoffs of selecting either a flexible, low modulus adhesive system, or a rigid / stiff, lower CTE product. Often, early on the selection process, it may help to run mock up trials with both types of adhesives (rigid / stiff, lower CTE & flexible / toughened, higher CTE), since, geometries, substrates, and the conditions can vary from application to application.
The following table lists some of Master Bond’s low CTE epoxies which offer a rigid cure with high modulus, as well as higher CTE epoxies which offer a flexibilized / toughened cure with lower modulus:
Product | CTE at room temperature, ppm/C | Elongation | Tensile Modulus, psi | Lap Shear Strength, psi |
EP42HT-2Med | 9-12 | <1% | 550,000-650,000 | 700-900 |
EP40Med | 55-60 | 80-90% | 25,000-50,000 | 1,600-1,800 |
EP17HTND-CCM | 20-25 | 1-2% | >600,000 | 2,400-2,600 |
EP21TDC-2LO | 80-90 | 25-35% | 20,000-30,000 | 600-800 |
EP42HT-3AO | 13-16 | <1% | >750,000 | 900-1,100 |
EP29LPHE | 50-55 | 100-150% | 10,000-20,000 | 1,400-1,600 |