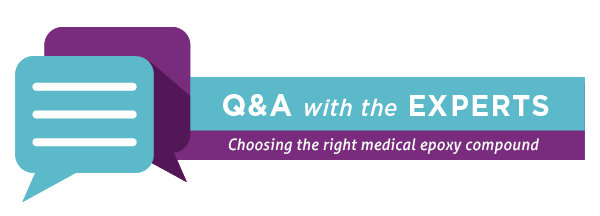
Join Venkat Nandivada and Nina Glaser from our technical and customer service teams, respectively, for an update to the selection process of adhesives for medical device applications. Learn the difference between applications dealing with disposable and reusable medical devices and how to overcome the challenges of each. See how adhesive technology is aiding medical device manufacturing, especially with respect to the impact of global pandemics, like the one created by Covid-19 that we are experiencing today.
NG: What are some of the issues medical device engineers face with respect to manufacturability requirements?
VN: Medical device engineers not only have to contend with demanding application requirements—such as high bond strength, thermal performance and chemical resistance—but they have the added challenge of working within a strict regulatory environment. They must choose materials that are biocompatible and can withstand aggressive sterilization methods, which sometimes have conflicting end-use and manufacturability requirements. Special attention needs to be placed on gap filling properties, joining dissimilar substrates, appearance and proper curing techniques.
NG: What should the engineer know about biocompatible adhesives?
VN: A common misconception is that FDA regulations require that adhesives be tested for biocompatibility before they can be incorporated in a medical device. In truth, the FDA actually considers only the biocompatibility of the finished medical device, not its individual materials. Engineers have the freedom to select and combine materials as they please, as long as the finished device passes muster with the FDA.
In practice, sticking with materials known to be biocompatible makes it more likely that the finished device will be biocompatible. So design and process engineers rightly favor adhesives and other materials that have been “pre- screened” by passing strict industry standard biocompatibility tests. The most widely accepted test standards are the USP Class VI for biocompatibility, and ISO 10993-5 requirements for cytotoxicity.
NG: How do the sterilization methods affect the medical device and what is the impact of the sterilization on the adhesive used?
VN: To answer this question, I’d like to focus on two broad categories of medical devices, disposable and reusable. Let’s start with disposable devices. These are typically bulk sterilized a single time as part of their manufacturing process. EtO and gamma radiation have traditionally been the methods of choice, and neither pose a degradation problem for medical adhesives at that level of exposure. The same goes for newer bulk sterilization methods, such as hydrogen peroxide and electron beam. In these disposable applications, a wide variety of USP Class VI rated epoxies, UV-curables, cyanoacrylates, and silicone adhesives can fit the bill. The adhesive choice will depend on the overall application requirements, and not just sterilization resistance.
NG: What about reusable devices?
VN: The vast majority of reusable devices will have to endure multiple trips through an autoclave, some even hundreds of times. Or they may be repeatedly treated with polymer-unfriendly chemical sterilizing agents. For these devices, aggressive sterilization does indeed limit the number of suitable adhesives and polymer substrate materials. Epoxies typically hold up best to chemical, moisture and high temperatures. So the majority of autoclave-tolerant adhesives tend to be an epoxy of one kind or another, although other adhesive chemistries can hold up in the autoclave as well if the cycles are more limited.
Epoxies typically hold up best to chemical, moisture and thermal resistance. So the majority of autoclave-tolerant adhesives tend to be an epoxy of one kind or another, although other adhesive chemistries can hold up in the autoclave as well if the cycles are more limited.
NG: What type of application issues do engineers need to reconcile to facilitate assembly?
VN: Here again, the answer may depend on whether the device is reusable or disposable. If you assume that disposables have the highest manufacturing volumes, that would translate to the need for the most productive medical adhesives available. For these applications, there are many USP Class VI and ISO10993-5 rated adhesives that require little or no complex mixing, are easy to apply, cure quickly, and resist common sterilization methods. Some of the popular choices for these high-volume applications are cyanoacrylates, UV-curables and certain one-part epoxies.
With reusable devices, epoxies and other adhesives that are best at withstanding multiple autoclave cycles are not always the fastest or easiest to use on the shop floor. They don’t cure as fast as cyanoacrylates or uv-curables. They may have mix ratios less straightforward than a simple 1 to 1. They may require fixturing and a heat cure. These issues are by no means insurmountable, and medical device makers successfully work with these adhesives every day.
NG: Are there any other productivity issues to consider?
VN: We often hear that engineers typically favor adhesives that cure at room temperature to avoid the time and expense of a heat cure. In medical applications, where quality and performance are paramount, adhesives formulated to cure at room temperature will still get the benefit from a heat cycle. In other words, mechanical and physical properties that are good after a room temperature cure are even better after a heat cycle, and medical devices need to be the best they can be.
NG: How do you see the changes in medical device manufacturing affecting the field of adhesive technology over the next decade?
VN: With the impact of global pandemics like the one created by COVID-19, there is a critical requirement to improve molecular diagnostic instruments, manufacture ventilators, increase the number of ICU equipment such as CT scanners, Xray equipment, monitors, pumps, and smart beds. In the pursuit to do so, there will be a need to choose adhesives, sealants, coatings, and encapsulants which are not only biocompatible and sterilization resistant, but also capable of resisting disinfectant chemicals or anti-microbial/anti-bacterial chemicals. Additionally, with the rise of medical electronic systems, the design of medical electronics is becoming more sophisticated. Whether it’s for a massive MRI or a tiny implantable circuit, advanced assembly and packaging technologies are critical for achieving size, and power requirements while ensuring reliable performance, and keeping patients safe.
The combination of increasingly complex assemblies and exacting quality requirements is compelling design engineers to be exceptionally careful when selecting components, materials, and packaging technologies for medical electronic devices.
Widely Used USP Class VI Approved Products
![]() |
EP42HT-2Med Low viscosity, two part epoxy with outstanding chemical resistance. Passes USP Class VI biocompatibility tests. Capable of withstanding repeated sterilization cycles including radiation, EtO, chemical sterilants, autoclaving. Serviceable from -60°F to +450°F. Cures at room or elevated temperatures. Available in amber-clear and black colors. Castable in thicknesses up to 2-3 inches. |
![]() |
EP62-1Med Two part epoxy requiring moderate heat curing (80-120°C). Meets USP Class VI biocompatibility specifications. Superb resistance to repeated autoclaving along with excellent adhesion to high temperature plastics such as Ultem, PEEK, etc. Exceptionally long working life. Outstanding electrical insulation properties. Serviceable from -60°F to +450°F. |
![]() |
UV10TKMed Biocompatible, high viscosity, UV curable compound. Optically clear. Glass transition temperature of more than 140°C. Rapid curing, no mix system. Withstands repeated sterilization. Meets USP Class VI and ISO 10993-5 cytotoxicity testing requirements. Serviceable from -60°F to +450°F. |
![]() |
EP21AOLV-2Med Meets USP Class VI requirements and passes ISO 10993-5 tests for cytotoxicity. Smooth flowable consistency. Thermally conductive//electrically insulative. Can be used for bonding, sealing, coating, encapsulation. One to one mix ratio. Cures at room temperature. Resists EtO, radiation, and chemical sterilants. Serviceable from -60°F to +250°F. |
![]() |
EP21LVMed Biocompatible two component epoxy adhesive, sealant, coating, encapsulant. Passes USP Class VI testing. Thermal cycling resistant. Can withstand exposure to EtO, radiation, chemical sterilants. Low viscosity. Easy to apply. Serviceable from -65°F to +250°F. |
![]() |
EP3HTSMed One part, silver conductive epoxy adhesive. USP Class VI approved. Rapid cures at elevated temperatures. Thixotropic paste. Serviceable from -60°F to +400°F. High shear strength. Excellent thermal and electrical conductivity. Exceptionally low resistivity. |
![]() |
MasterSil 151Med Medical grade, USP Class VI approved silicone. Addition type cure system. Optically clear. Low outgassing. Offers ambient or elevated temperature cures. Excellent for potting and encapsulation applications. Low shrinkage upon cure. Resists gamma radiation, EtO and various chemical sterilants. Serviceable from -65°F to +400°F. |
![]() |
UV15DC80Med USP Class VI approved one component UV and heat curable epoxy. Passes ISO 10993-5 cytotoxicity testing. Cures at temperatures as low as 80°C. Moderate viscosity. Minimal shrinkage upon cure. Capable of withstanding liquid sterilants, radiation, autoclaving. Serviceable from -60°F to +400°F. |