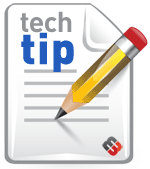
In order to understand the importance of the volume dispensed to create an underfill fillet, let us first take a look at what an adhesive fillet looks like.
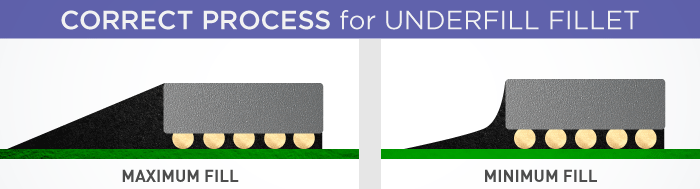
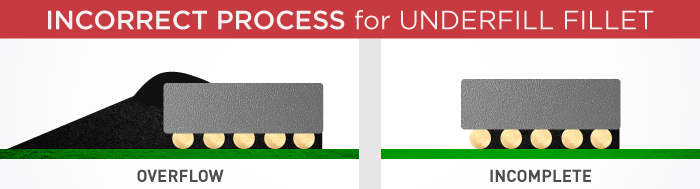
The formation of an optimal fillet as shown below provides not only additional support, but also accounts for slight misalignments between substrates. However, care should be taken that neither an incomplete fill nor an excess amount of adhesive is applied, since both defects are detrimental for a bond joint. In the case of an incomplete fill, it might not provide enough structural support. On the other hand, if there is an excess amount of adhesive, this might cause the adhesive to creep up to the top of one of the substrates. This might lead to an additional clean up step, and in turn increase the processing times, as well as create manufacturing bottlenecks.
Typically, for an underfill fillet, the gaps between a die (or flip-chip), and the solder balls underneath soldered to a PCB substrate, need to be encapsulated or filled to provide mechanical reinforcement against harsh thermal and mechanical stresses. In order to achieve this, there is a narrow window for the volume of adhesive that can be dispensed to form the “ideal” fillet. The minimum amount is determined based on the absolute minimum fillet height and width such that the underfill volume does not lead to an incomplete fill. Similarly, the maximum volume can be determined such that the underfill does not creep up over the die and end up covering it. These can either be determined through experiments on mock-ups or they can be calculated based on the exact size of the components, the pitch size, and the volume occupied by the solder balls or the components underneath the flip chip.
There are different types of equipment available, which can help precisely and accurately apply underfill materials with viscosities ranging from a few 100 cps to a few 100,000 cps. Typically, for capillary flow underfills a lower viscosity compound with a relatively long working life is preferred, which might be either applied through conventional needle dispensing or jetting techniques. On the other hand for a non-flow type underfill, thixotropic compounds, which are non-sag after being dispensed, tend to be preferred.